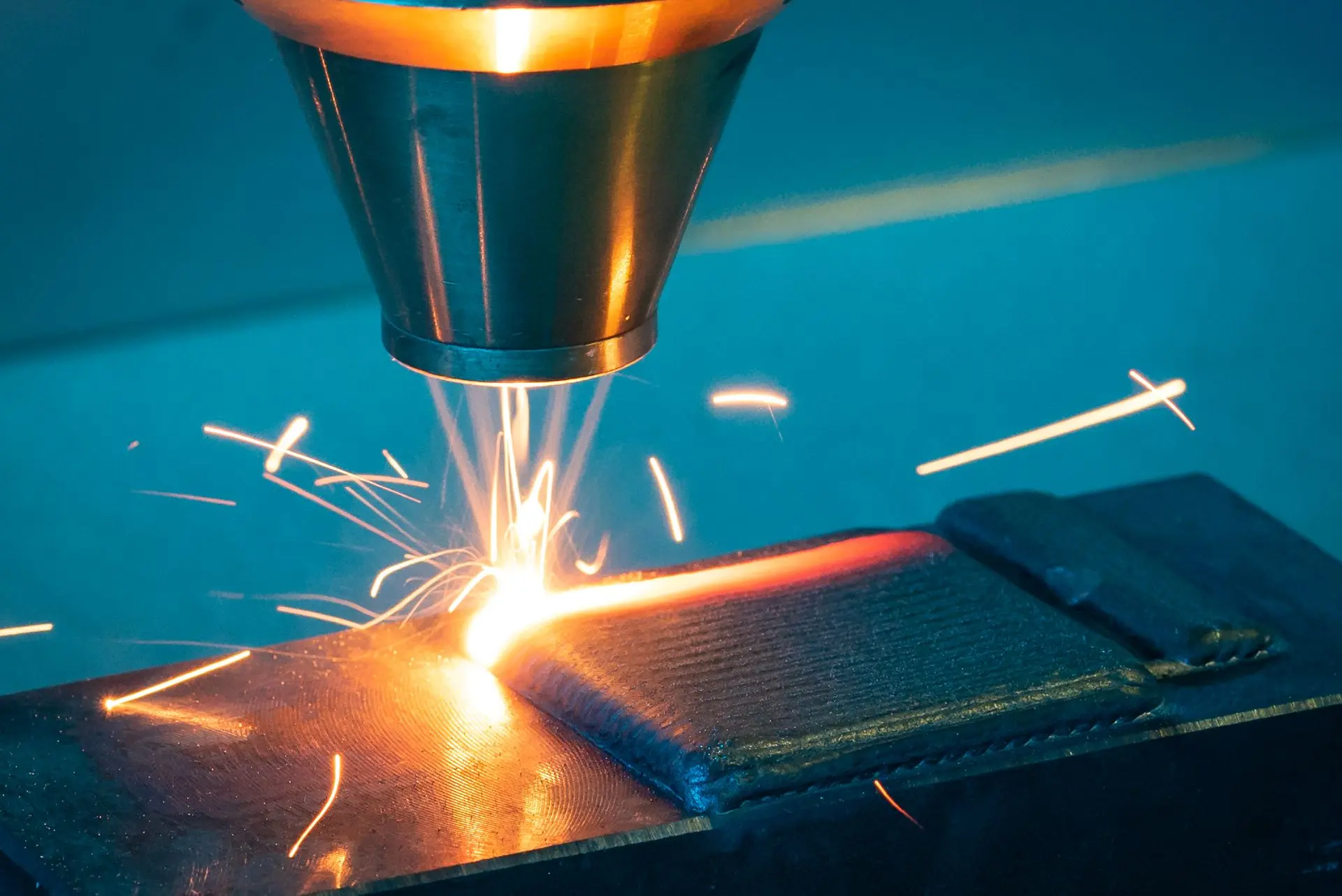
Laser cladding is a material deposition process that uses a laser source to melt and adhere metal powder or wire locally using a dedicated nozzle.
The process features high speeds and minimal deformation, which results in a metallurgical bond between the deposited material and the substrate. This coating is more durable than the one produced using the Thermal Spray technique and is not harmful to health like the hard chrome plating.
The main areas of application are mould repair, 3D printing and the imparting of high mechanical-corrosive properties to parts that are subject to wearing.
Cladding
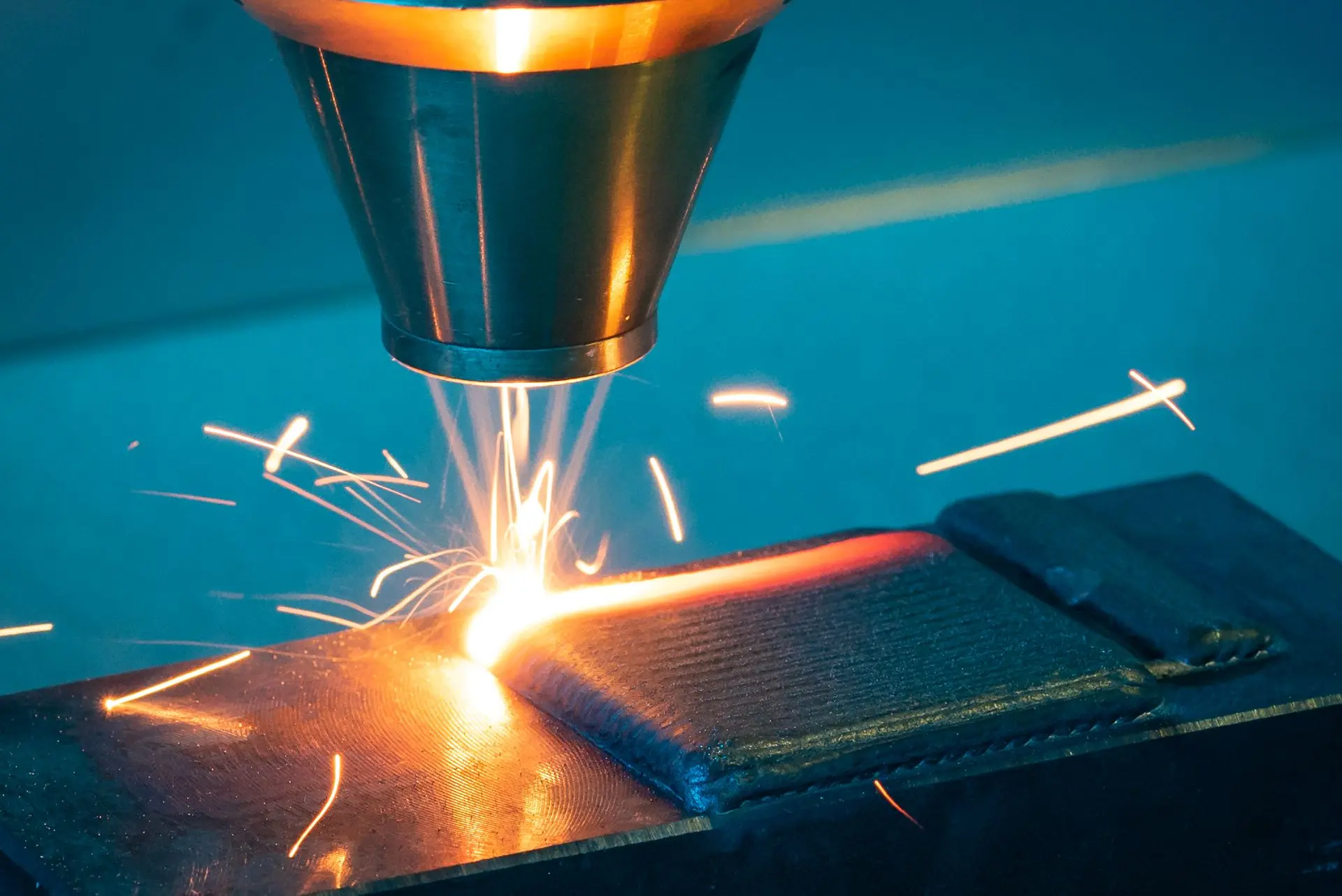
Laser cladding is a material deposition process that uses a laser source to melt and adhere metal powder or wire locally using a dedicated nozzle.
The process features high speeds and minimal deformation, which results in a metallurgical bond between the deposited material and the substrate. This coating is more durable than the one produced using the Thermal Spray technique and is not harmful to health like the hard chrome plating.
The main areas of application are mould repair, 3D printing and the imparting of high mechanical-corrosive properties to parts that are subject to wearing.
Cladding
In cladding, lasers are used to apply a layer of material onto a substrate to enhance its surface properties, such as improving wear resistance, corrosion resistance, and overall durability. The most commonly used types of lasers for cladding are fiber lasers, CO2 lasers, and diode lasers, each offering specific advantages depending on the application.
Fiber lasers are widely utilized in cladding due to their excellent beam quality and high power density. Their ability to focus on small areas with precision makes them ideal for applications that require high-quality, controlled cladding. Fiber lasers are particularly effective for metals and alloys, providing a high degree of control during the cladding process to ensure uniform coating and optimal adhesion.
CO2 lasers are another popular choice for cladding, especially when deeper penetration or larger areas need to be clad. These lasers have a high power output, which allows them to efficiently melt the cladding material and create strong, durable bonds. CO2 lasers are commonly used in industries such as aerospace, automotive, and manufacturing, where complex components require robust cladding solutions.
Diode lasers, though less common, are sometimes used in cladding for their ability to provide localized, precise heat. They are particularly beneficial for high-throughput cladding processes and for applications where energy efficiency is a priority. Diode lasers are suitable for thinner coatings or surface treatments, offering good control while minimizing the heat-affected zone.
Each of these laser types is selected based on the specific requirements of the cladding process, such as the type of material, desired coating thickness, and the overall application. Whether it's the precision of fiber lasers, the power of CO2 lasers, or the efficiency of diode lasers, each provides unique benefits that help ensure the success of the cladding operation.
In cladding, lasers are used to apply a layer of material onto a substrate to enhance its surface properties, such as improving wear resistance, corrosion resistance, and overall durability. The most commonly used types of lasers for cladding are fiber lasers, CO2 lasers, and diode lasers, each offering specific advantages depending on the application.
Fiber lasers are widely utilized in cladding due to their excellent beam quality and high power density. Their ability to focus on small areas with precision makes them ideal for applications that require high-quality, controlled cladding. Fiber lasers are particularly effective for metals and alloys, providing a high degree of control during the cladding process to ensure uniform coating and optimal adhesion.
CO2 lasers are another popular choice for cladding, especially when deeper penetration or larger areas need to be clad. These lasers have a high power output, which allows them to efficiently melt the cladding material and create strong, durable bonds. CO2 lasers are commonly used in industries such as aerospace, automotive, and manufacturing, where complex components require robust cladding solutions.
Diode lasers, though less common, are sometimes used in cladding for their ability to provide localized, precise heat. They are particularly beneficial for high-throughput cladding processes and for applications where energy efficiency is a priority. Diode lasers are suitable for thinner coatings or surface treatments, offering good control while minimizing the heat-affected zone.
Each of these laser types is selected based on the specific requirements of the cladding process, such as the type of material, desired coating thickness, and the overall application. Whether it's the precision of fiber lasers, the power of CO2 lasers, or the efficiency of diode lasers, each provides unique benefits that help ensure the success of the cladding operation.