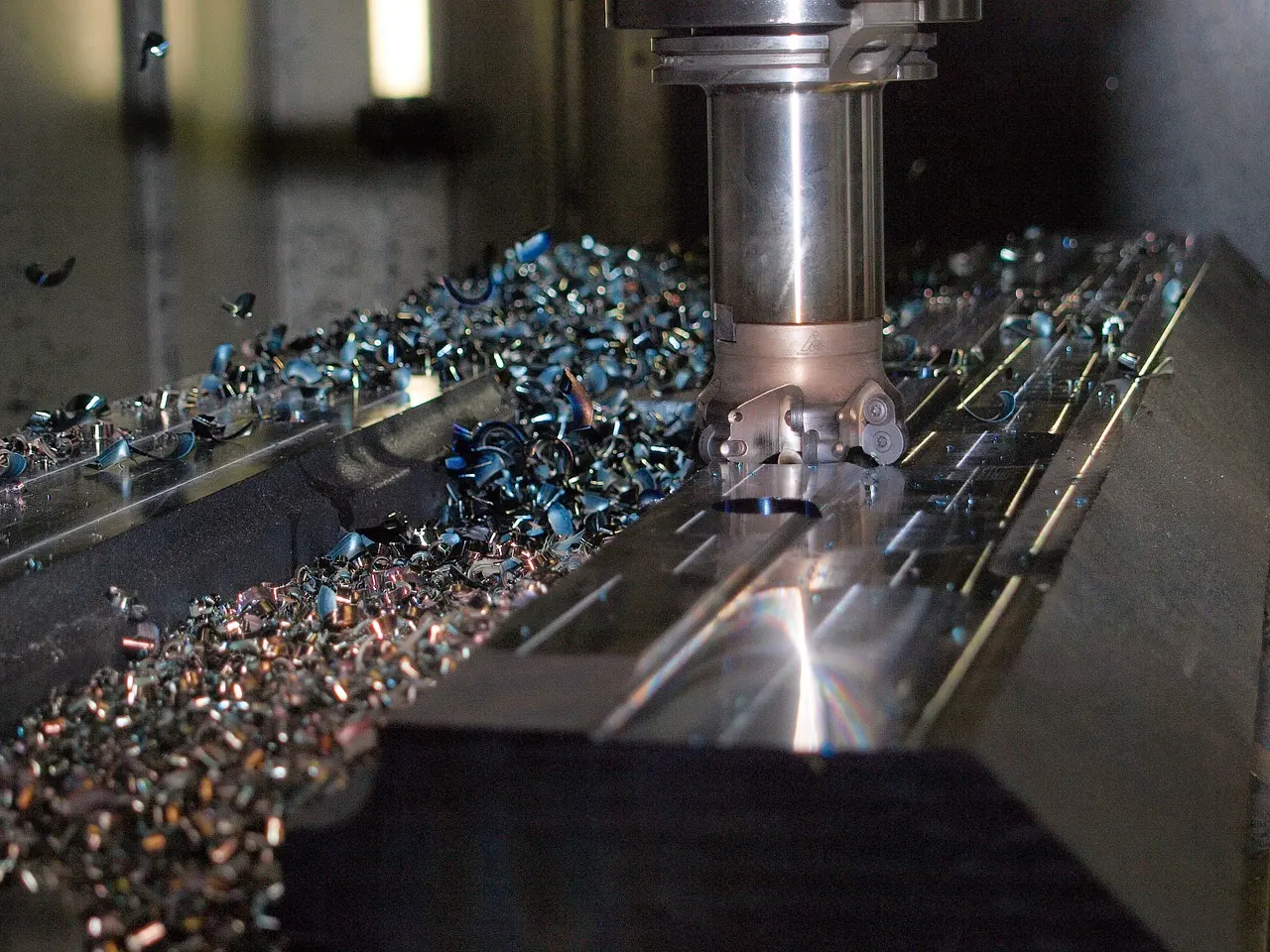
Micromachining is a manufacturing process where material is removed from a workpiece on a micrometer scale. This technique is pivotal in producing microcomponents with high precision and crucial in industries like aerospace, medical devices, and electronics.
In micromachining, tools and methods are meticulously designed to handle dimensions and tolerances that conventional machining can’t achieve, marking a significant leap in fabrication capabilities.
Laser micromachining is different from classic laser processing because it involves the use of very short pulsed lasers, allowing 'cold' processing of the material without heat input. Parts made with this technology often do not require further processing, simplifying the production process.
Micromachining
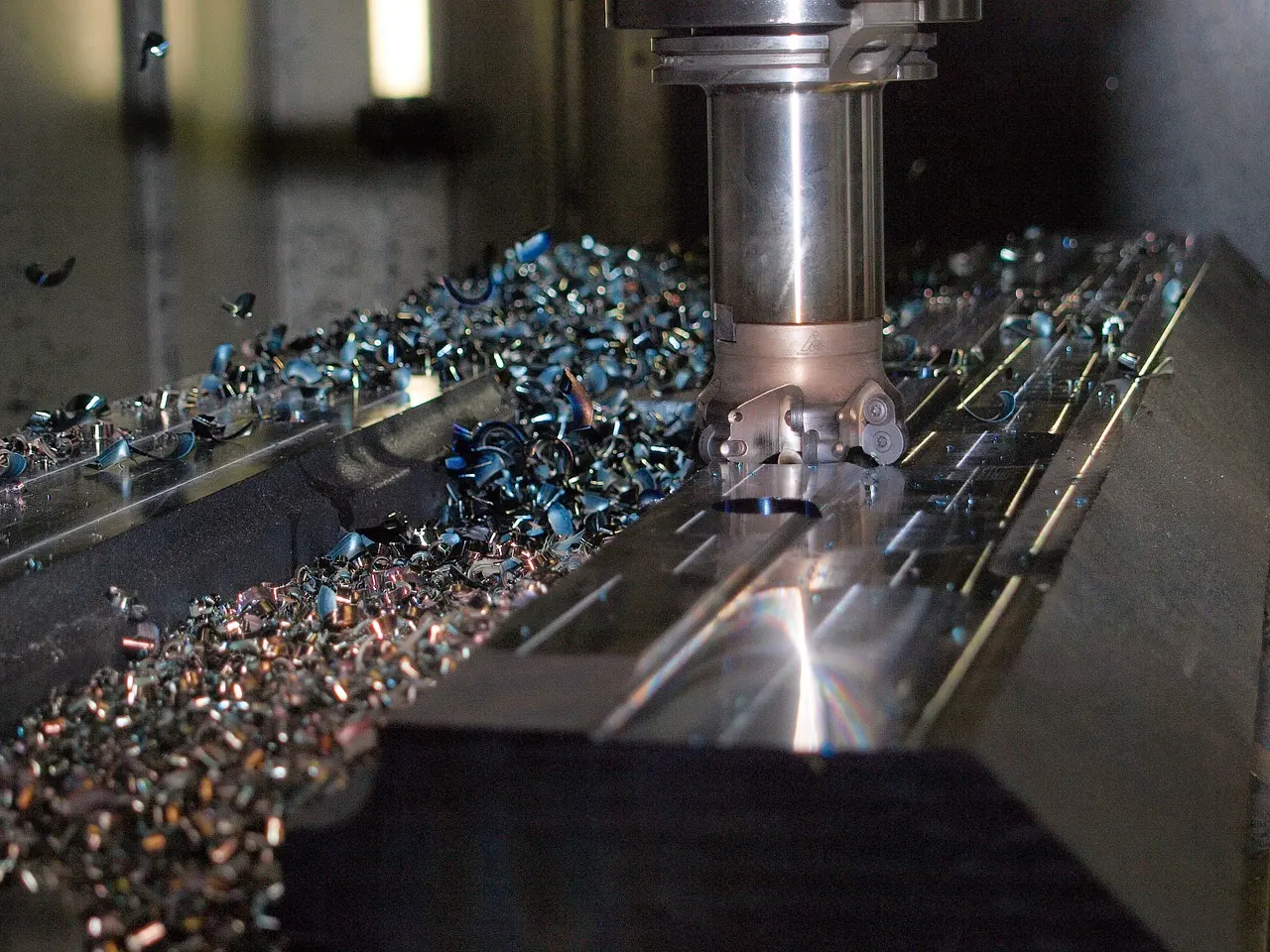
Micromachining is a manufacturing process where material is removed from a workpiece on a micrometer scale. This technique is pivotal in producing microcomponents with high precision and crucial in industries like aerospace, medical devices, and electronics.
In micromachining, tools and methods are meticulously designed to handle dimensions and tolerances that conventional machining can’t achieve, marking a significant leap in fabrication capabilities.
Laser micromachining is different from classic laser processing because it involves the use of very short pulsed lasers, allowing 'cold' processing of the material without heat input. Parts made with this technology often do not require further processing, simplifying the production process.
Micromachining
In micromachining, lasers are used for precise, high-accuracy processing of small features and intricate designs on materials. The types of lasers commonly used for micromachining include fiber lasers, femtosecond lasers, CO2 lasers, and excimer lasers, each chosen for their specific capabilities in terms of precision, material interaction, and processing speed.
Fiber lasers are widely used in micromachining due to their excellent beam quality, high power density, and ability to focus on very fine details. Fiber lasers are ideal for machining metals, ceramics, and plastics, allowing for precise cutting, engraving, and drilling. They are particularly effective for applications in industries like electronics, automotive, and aerospace, where high-precision work is critical.
Femtosecond lasers are a type of ultrafast laser that emits pulses in the femtosecond range (one quadrillionth of a second). These lasers are used in micromachining because they offer extremely fine precision and minimal heat-affected zones. femtosecond lasers are ideal for applications that require high-quality, damage-free processing of materials like glass, silicon, and biomaterials. They are commonly used in applications such as micro drilling, micro cutting, and surface structuring where precision is paramount.
CO2 lasers are used in micromachining for processing materials like plastics, wood, rubber, and certain types of metals. CO2 lasers can achieve high precision in cutting and engraving thin materials and are especially useful in applications where high-quality marks or cuts are required. These lasers are widely used for creating intricate patterns or designs in industries like packaging and consumer goods.
Excimer lasers are another type of laser used in micromachining, particularly for applications that require precise, high-quality material removal with minimal thermal effects. Excimer lasers are ideal for drilling fine holes, patterning thin films, and cutting intricate microstructures in materials like polymers, ceramics, and semiconductors. These lasers are commonly used in the electronics and semiconductor industries for microfabrication and component assembly.
Each of these lasers is chosen for its ability to provide highly precise, controlled processing in micromachining, with the selection depending on the material being worked on, the level of precision required, and the specific application. Fiber lasers and femtosecond lasers are particularly popular for their ability to handle delicate, high-precision tasks, while CO2 lasers and excimer lasers are used for specific applications in non-metallic materials and microfabrication.
In micromachining, lasers are used for precise, high-accuracy processing of small features and intricate designs on materials. The types of lasers commonly used for micromachining include fiber lasers, femtosecond lasers, CO2 lasers, and excimer lasers, each chosen for their specific capabilities in terms of precision, material interaction, and processing speed.
Fiber lasers are widely used in micromachining due to their excellent beam quality, high power density, and ability to focus on very fine details. Fiber lasers are ideal for machining metals, ceramics, and plastics, allowing for precise cutting, engraving, and drilling. They are particularly effective for applications in industries like electronics, automotive, and aerospace, where high-precision work is critical.
Femtosecond lasers are a type of ultrafast laser that emits pulses in the femtosecond range (one quadrillionth of a second). These lasers are used in micromachining because they offer extremely fine precision and minimal heat-affected zones. femtosecond lasers are ideal for applications that require high-quality, damage-free processing of materials like glass, silicon, and biomaterials. They are commonly used in applications such as micro drilling, micro cutting, and surface structuring where precision is paramount.
CO2 lasers are used in micromachining for processing materials like plastics, wood, rubber, and certain types of metals. CO2 lasers can achieve high precision in cutting and engraving thin materials and are especially useful in applications where high-quality marks or cuts are required. These lasers are widely used for creating intricate patterns or designs in industries like packaging and consumer goods.
Excimer lasers are another type of laser used in micromachining, particularly for applications that require precise, high-quality material removal with minimal thermal effects. Excimer lasers are ideal for drilling fine holes, patterning thin films, and cutting intricate microstructures in materials like polymers, ceramics, and semiconductors. These lasers are commonly used in the electronics and semiconductor industries for microfabrication and component assembly.
Each of these lasers is chosen for its ability to provide highly precise, controlled processing in micromachining, with the selection depending on the material being worked on, the level of precision required, and the specific application. Fiber lasers and femtosecond lasers are particularly popular for their ability to handle delicate, high-precision tasks, while CO2 lasers and excimer lasers are used for specific applications in non-metallic materials and microfabrication.