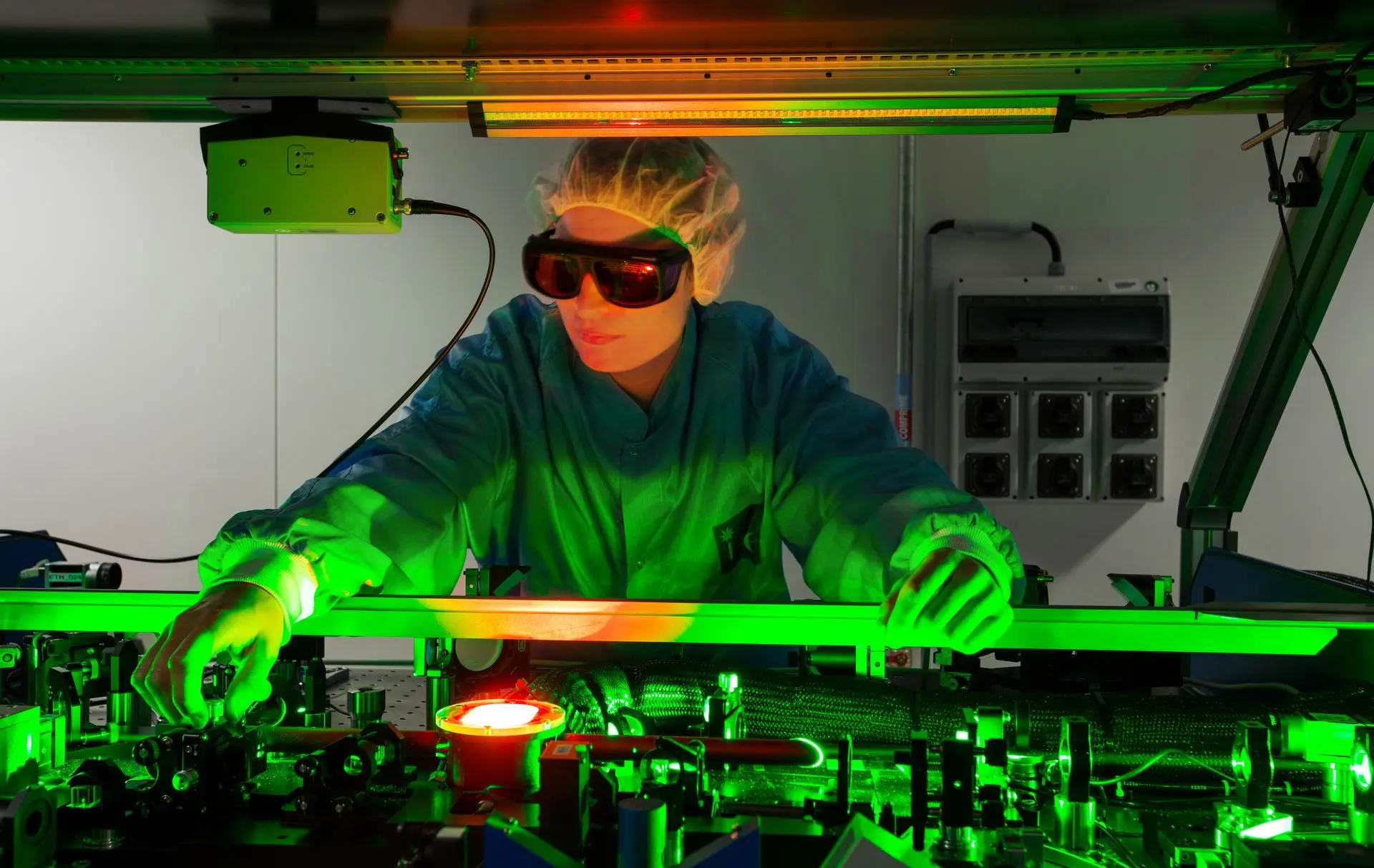
Testing and inspection are the final steps in any production process for machines or complex systems in general. These two operations play a fundamental role in verifying that a machine or process works according to design specifications and also complies with all safety regulations.
With specific reference to machines that include a laser, it is essential to do a complete characterization of the beam (power, energy, spatial profile of the pulse, spot size) to certify the correct performance of the entire machine.
Regarding in-line processes, it is essential to check the quality of the product in real time after each processing step to detect as soon as possible any defects in conformity or the presence of contaminants.
Testing and Inspection
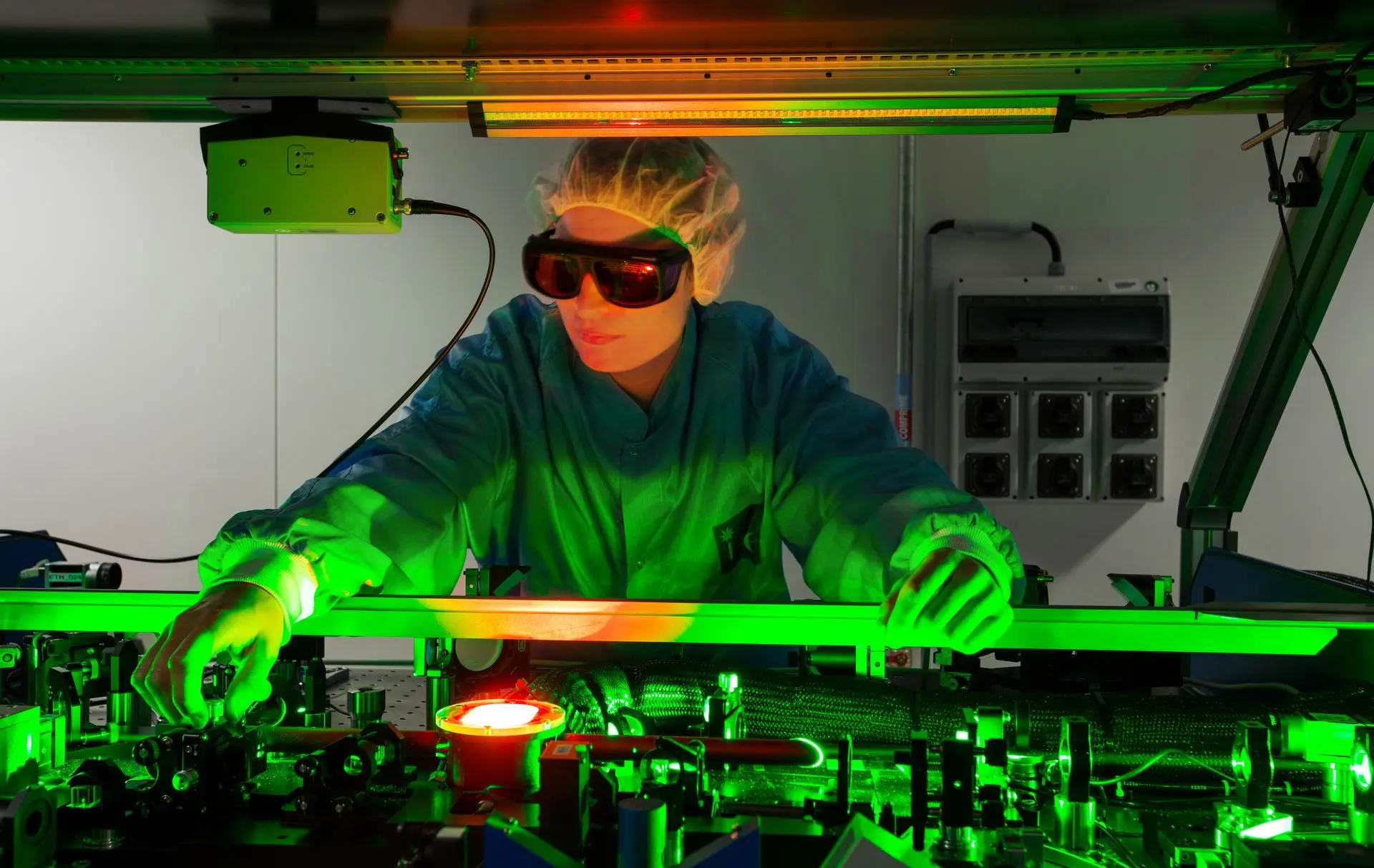
Testing and inspection are the final steps in any production process for machines or complex systems in general. These two operations play a fundamental role in verifying that a machine or process works according to design specifications and also complies with all safety regulations.
With specific reference to machines that include a laser, it is essential to do a complete characterization of the beam (power, energy, spatial profile of the pulse, spot size) to certify the correct performance of the entire machine.
Regarding in-line processes, it is essential to check the quality of the product in real time after each processing step to detect as soon as possible any defects in conformity or the presence of contaminants.
Testing and Inspection
In testing and inspection, lasers are used for precise, non-contact measurement, defect detection, and quality control across a variety of industries. Common types of lasers employed in these applications include diode lasers, fiber lasers, CO₂ lasers, and He-Ne lasers, each chosen based on the material, measurement type, and environment.
Diode lasers are widely used for laser triangulation, surface profiling, and dimension measurements due to their compact size, efficiency, and availability in different wavelengths. They are ideal for real-time inspection on production lines and are commonly found in automotive, electronics, and packaging industries.
Fiber lasers are used when high precision and stability are required, particularly in 3D scanning, micro-inspection, and non-destructive testing. Their excellent beam quality and power output make them suitable for inspecting metal surfaces, welds, and composite materials.
CO₂ lasers are often used for surface defect detection and marking inspection on non-metallic materials like plastics, paper, and glass. Their longer wavelength is effective for interacting with organic materials, making them valuable in textile, food, and pharmaceutical industries.
The choice of laser in testing and inspection depends on the application’s resolution, material type, and required inspection speed. Diode and fiber lasers are favored for versatility and industrial use, CO₂ lasers for inspecting non-metals.
In testing and inspection, lasers are used for precise, non-contact measurement, defect detection, and quality control across a variety of industries. Common types of lasers employed in these applications include diode lasers, fiber lasers, CO₂ lasers, and He-Ne lasers, each chosen based on the material, measurement type, and environment.
Diode lasers are widely used for laser triangulation, surface profiling, and dimension measurements due to their compact size, efficiency, and availability in different wavelengths. They are ideal for real-time inspection on production lines and are commonly found in automotive, electronics, and packaging industries.
Fiber lasers are used when high precision and stability are required, particularly in 3D scanning, micro-inspection, and non-destructive testing. Their excellent beam quality and power output make them suitable for inspecting metal surfaces, welds, and composite materials.
CO₂ lasers are often used for surface defect detection and marking inspection on non-metallic materials like plastics, paper, and glass. Their longer wavelength is effective for interacting with organic materials, making them valuable in textile, food, and pharmaceutical industries.
The choice of laser in testing and inspection depends on the application’s resolution, material type, and required inspection speed. Diode and fiber lasers are favored for versatility and industrial use, CO₂ lasers for inspecting non-metals.